Primary iPhone assemblers Foxconn and Pegatron are said to have been evaluating the ability of the company to shift production of Apple's mobile devices to the U.S., with the verdict mixed on if the move would be cost-effective.
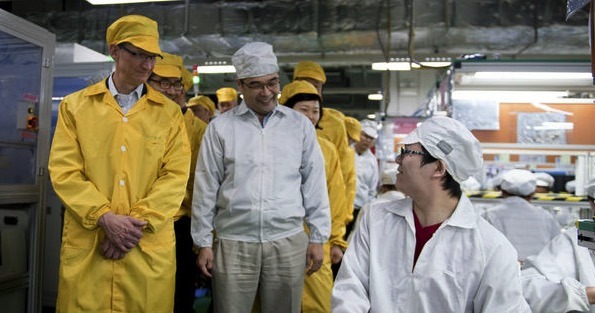
"Apple asked both Foxconn and Pegatron, the two iPhone assemblers, in June to look into making iPhones in the U.S.," a source told the Nikkei Asian Review. "Foxconn complied, while Pegatron declined to formulate such a plan due to cost concerns."
Reportedly, Foxconn Chief Executive Terry Gou was critical of the plan, saying that labor and other associated costs would more than double, should the plan come to fruition.
Pegatron was also reportedly tasked with developing a U.S. manufacture report, but declared the shift impossible due to costs.
A 35% cost increase, regardless if induced by labor and material shipping costs, or a tariff would likely passed on to consumers, making a $649 base-model iPhone retail for around $876.
The study was probably spawned because of potential political pressure and taxation for Apple promised by President Elect Donald Trump during campaigning for the office. Trump's campaign promise of a 35 percent tariff levied against products like the iPhone manufactured overseas, is presumed by the President Elect to give companies a significant economic incentive to bring manufacturing jobs back to the U.S.
"Although TSMC is very clear that it would be much more expensive to make chips outside of Taiwan, it's inevitable for the world's largest contract chipmaker to take 'Made in the U.S.' into consideration," said Sanford C. Bernstein analyst Mark Li. "The alternative is that it would lose Apple orders without moving to America."
Apple's stance on the matter
"To make iPhones, there will need to be a cluster of suppliers in the same place, which the U.S. does not have at the moment," Apple CEO Tim Cook said in an Dec. 2015 interview about a possible shift. "Even if Trump imposes a 45% tariff, it is still possible that manufacturers will decide to continue production overseas as long as the costs together with the tariffs are lower than the amount they need to spend on building and running production lines in the U.S."
A 35 percent cost increase, regardless if induced by labor and material shipping costs, or a tariff would likely passed on to consumers, making a $649 base-model iPhone retail for around $876.