After a few months of revenue boosted by Apple production demands, manufacturing partner Pegatron's CEO says that the company could build the "iPhone 7s" and "iPhone 8" in the U.S. if it is asked to -- but Apple would have to shoulder all of the company's costs for doing so.
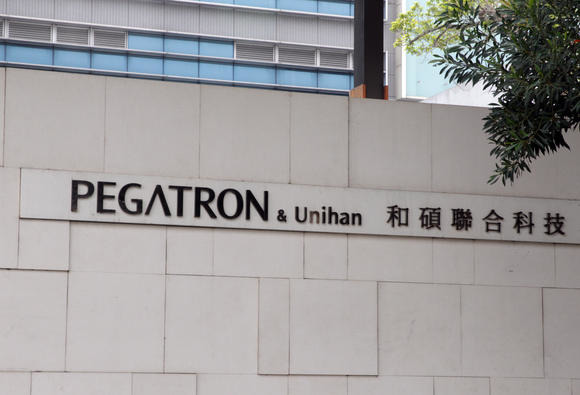
"As long as there is demand, whether the clients are American or Chinese, Pegatron already has its production lines in place," Pegatron CEO Liao Syh-jang said at an investor's conference to Focus Taiwan. "If Trump institutes his Made in America proposal, it will be fine for Pegatron as long the client is willing to absorb the costs."
Also at the conference, Liao reported that the company is pessimistic about revenue for the next few months, citing a weak laptop market as the major reason.
The production shift remarks echo similar ones the company made in January, but implies that a larger scale ramp-up is possible. At that time, Pegatron chairman TH Tung said that three to five times the manufacturing capacity could be added to its U.S. locations, but would have little impact on either the workforce, or Apple's total demand for the iPhone.
Neither the California or Indiana U.S. Pegatron facilities assemble goods for Apple at this time. Primary customers are HP and Dell. The companies also provide on-site service for some products in the areas that they serve.
When then-Presidential candidate Donald Trump threatened various countermeasures against companies building products overseas, and importing them, rather than relying on U.S.-based manufacture, Apple requested an impact statement from both Foxconn and Pegatron should a move be required. Foxconn developed a plan, and Pegatron reportedly did not, citing costs of the effort.
Trump's campaign promised a 35 percent tariff levied against products like the iPhone manufactured overseas. The plan, published in June, presumably will give companies a significant economic incentive to bring manufacturing jobs back to the U.S. if passed.
"To make iPhones, there will need to be a cluster of suppliers in the same place, which the U.S. does not have at the moment," Apple Chief Executive Tim Cook said in an Dec. 2015 interview about a possible shift. "Even if Trump imposes a 45 percent tariff, it is still possible that manufacturers will decide to continue production overseas as long as the costs together with the tariffs are lower than the amount they need to spend on building and running production lines in the U.S."
Assuming Apple has one phone priced at $700, the taxable income on the phone in the US is $280, because of production cost deductions and other factors generating $98 in tax for the U.S. at present rates.
Apple's expected overall tax rate is expected to fall to 20% versus the current 35% as a result of the Trump administration's tax reform "blueprint."
After reform, If the phone were manufactured in the US, the taxable income remains the same at $280, but the lower effective tax rate drops the owed taxes to $56. If the iPhone continues to be manufactured in China, the entire $700 is taxable, but at the lower 20%, ending up in an effective tax on the phone of $140.
How much labor and other costs associated with developing the supply line the U.S. would impact the phone production costs in the U.S. is not clear, but given corporate resistance to the idea, exceeds the difference in savings from the new tax proposal.
Regardless of the source of the cost increase, be it the expense of moving manufacture of the iPhone to the U.S. or keeping production overseas, any cost increase would likely be applied to consumers.