With the iPhone 5c, Apple was able to deliver a cost effective plastic smartphone with a "premium" feel by applying its considerable expertise in design, engineering and manufacturing to the project, a process highlighted during Tuesday's special media event.
Allaying concerns that the colorful iPhone 5c would feel "cheap," Apple introduced a device that can be described as substantial, an adjective not typically associated with a plastic smartphone. Equally impressive is the build process required to make a more affordable device without sacrificing the hallmark qualities that have become synonymous with the iPhone brand.
Apple's marketing chief Phil Schiller, who unveiled the 5c on Tuesday, briefly spoke of the company's efforts, though a video shown during the presentation offers a behind-the-scenes look at the advanced manufacturing tech. The short clip was subsequently uploaded to Apple's official YouTube channel.
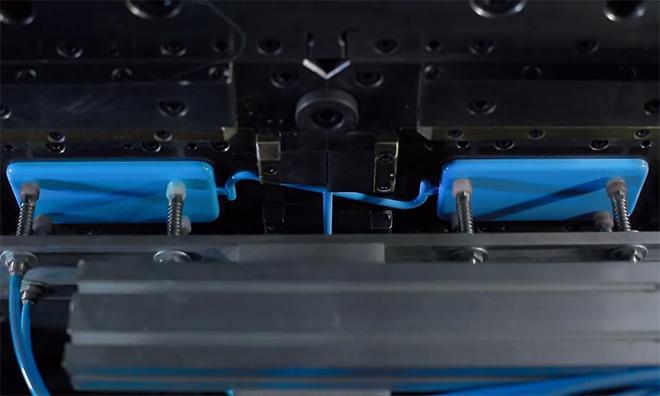
Polycarbonate pieces ready for steel frame insertion.
A common problem with many plastic smartphones is a lack of rigidity when compared to metal devices like the outgoing iPhone 5 its replacement, the iPhone 5s. To overcome this issue, Apple employs a new construction method that attaches a steel reinforced sub-structure to a hard-coated polycarbonate shell.
As in many Apple designs, a single component can serve more than one purpose, and the steel frame is no different. With the 5c, the metal structural element is also used as a multi-band antenna, a design scheme previously seen in the iPhone 4 and 4S. The steel skeleton is inserted into a single, seamless piece of polycarbonate and secured with a bonding agent.
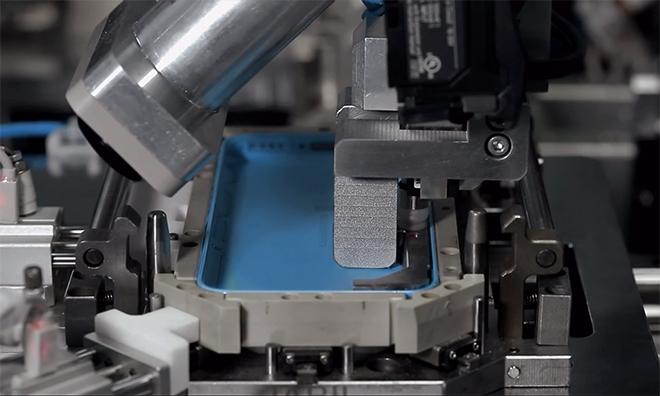
One side of steel reinforcement assembly being installed.
In the video, Apple's SVP of Design Jony Ive notes that the pairing of a steel reinforced frame and one-piece polycarbonate shell creates a "bespoke assembly."
Frame serves as a multi-band antenna.
Finishing off the frame is a metal rear plate that not only serves as a platform for the logic board and other circuitry, but adds rigidity to the structure as well.
From there, the shell moves on to a CNC machine that drills precise holes for the iPhone's physical controls. Because the manufacturing method is subtractive rather than additive, the integrity of the polycarbonate outer layer is less likely to be compromised.
CNC machine drilling out slots for physical controls.
Next up is a finishing process that requires multiple passes, including a clear lacquer hard coat which Ive says creates a durable and glossy surface. While the durability of the iPhone 5c has yet to be verified, a video from August claims to have put a "leaked" outer casing through a battery of scratch resistance tests. The outcome was largely favorable.
One step in a multi-pass polishing process.
Not shown in the video is the installation of functional components like the logic board and Gorilla Glass screen assembly, which itself adds even more stiffness.
"This whole process culminates in an extraordinarily rigid structure and a solid, dense feel that you would not expect from a plastic product," Ive says in the video.
AppleInsider was able to spend some hands on time with Apple's iPhone 5c, and we concur that the unit does feel substantial.
Preorders for the iPhone 5c will open on Sept. 13 ahead of a simultaneous iPhone 5s launch on Sept. 20. AppleInsider has learned that the iPhone 5s will not be available to order prior to in-store sales, possibly suggesting Apple anticipates supply constraints for the flagship device.