Apple has spent years and millions of dollars on automating its production lines with technology, and it has always reverted to using skilled human beings instead.
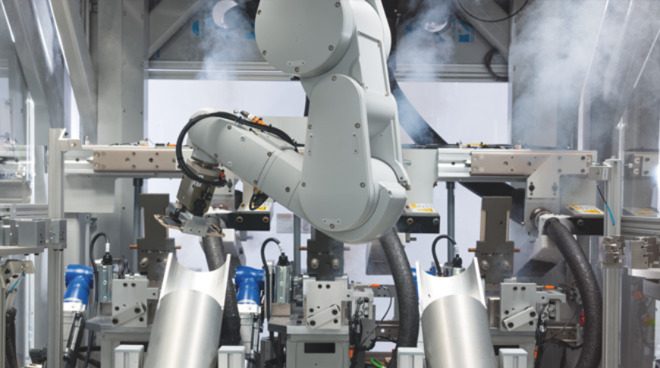
The most profitable technology company in the world, and arguably the most technologically advanced firm in history, won't use automation to make its products. Apple has repeatedly tried to build machines to build its machines, but in every case bar its recycling plans, it has failed -- and reverted to using human beings instead of robots.
"Robotics and automation is fantastic and amazing when it works," David Bourne told The Information when discussing his time working with Apple supplier Foxconn. "But when something breaks, God knows what happens."
Bourne, who is now principle systems scientist at the Robotics Institute at Carnegie Mellon University, used to work with Foxconn on multiple automation projects that had been intended to produce Apple's products.
It was Foxconn that pressed Apple on automation, and it was also Foxconn that impressed Apple on the idea. In 2012, Apple executives including Tim Cook were reportedly in China to see the results of an experimental production line. It was built to assemble the iPad by robots and showed the parts being cut, polished and then partially assembled into the final product.
Terry Guo, then chairman of Foxconn, reportedly told Apple that his firm's assembly lines would contain one million robots within two years.
Seven years on, in 2019, Foxconn was using just 100,000 robots across all of its manufacturing. Neither Foxconn nor Apple would comment publicly about why the automation was so much lower than predicted, but according to The Information, sources say it's down to dissatisfaction by Apple.
Apple's own automation teams
Seemingly as a result of Foxconn's original efforts, Apple launched its own secret robotics lab in 2012, based around six miles from Apple Park. It housed a team of automation specialists and robotics engineers who initially tried mimicking the iPad automatic production line.
The iPad Air - used by hands, made by hands.
They were given the target of reducing the amount of human labor needed by half. Specifically, Apple wanted to be able to cut 15,000 workers from the production line, which represents about 50% of the number of workers used at key times.
It didn't work. Typical problems that arose include how Apple's use of glue required precision the machinery couldn't reliably match. And the tiny screws needed required the automation to correctly pick and position them but that same automation couldn't detect problems the way a human hand could.
This lab was abandoned in 2018, although reportedly some of its work was picked up and continued by other parts of Apple. It wasn't the only department working on the project -- and arguably wasn't the biggest failure.
That title goes to the millions of dollars spent automating production of what would become the MacBook in 2015. That automated production line was started the year before in 2014, but persistent failures meant not only was it also abandoned, but that MacBook itself was postponed by some months.
MacBook
The attempt to automate the production of the MacBook went beyond a test department in Cupertino. The equipment was installed in a factory in China, and it was intended to assemble the screen, the keyboard, and the trackpad into the MacBook's casing.
Reportedly, though, there were problems with even the conveyor belt that moved parts along the line. It was erratic, it was sometimes slow, but the greatest issue was that parts along the line kept breaking down.
The MacBook was delayed to 2015 because of automation failures
What was worse, it wouldn't always be clear that something had gone wrong. "If things stop working, the automation can't detect that all the time and repair it," Bourne told The Information.
Insurmountable issues
If any firm were capable of fixing a technology problem, it would surely be Apple, but alongside technical issues there were more fundamental ones. Most specifically, since Apple redesigns its major hardware in at least some way every year, it would also have to redesign the automated factory lines.
Compared to that, training workers on new designs is vastly easier and quicker.
Plus, one reason both Foxconn and Apple were interested in automation is that as well as being dependent on workers, that dependency fluctuates greatly. Foxconn was having problems recruiting enough staff for the peak periods just after, say, an iPhone launch.
Automation would theoretically reduce that problem, but Apple already has a way of removing it. When it needs to, Apple is currently able to switch production to other companies. If there's a problem or if more production is needed, it has alternative sources it can leverage.
If those sources had to have annually-updated automated production lines installed by Apple, the company would not have the flexibility it has now.
So more than overcoming technical issues, it is the series of business rationales that are likely to keep Apple using human labor in the production of its machines. It's not just Apple, either, as both Tesla and Boeing have famously attempted and abandoned automation for the same reasons.